How I Saved My Client a Bundle With an LED Lighting Retrofit
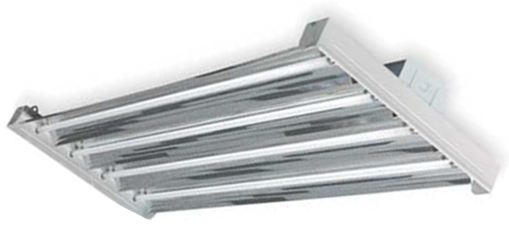
The client (a group of attorneys) had just purchased a four-story 45,000 ft² historic office building and they’re in the process of renovating. It contained 295 4-foot troffers, each containing four T-12 fluorescent tubes. We all know T-12s are so inefficient (approximately 45 watts/tube counting the ballasts) that in 2012, the DOE ruled they can no longer be manufactured in the U.S or imported from offshore manufacturers. In addition to wasting energy, T12s also flicker and hum, create toxic mercury & PCB’s in their waste stream and provide poor quality light.
The architectural firm originally called for new T-5 fixtures, but since the new owners wanted to save money both upfront on installation costs and over the long term on operational costs, the project manager called me for an alternative proposal. I’m a reseller for a line of American-made LED tubes and fixtures and knew we could save them money on both counts by re-using the old fixtures after simply retrofitting them with LED tubes. Here’s’ what we did:
The interior demolition crew removed all the old troffers and stored them in a single room. Once the new plans were finished, it was determined 295 of the troffers would be used again. The old T-12 lamps were removed and disposed of and I ordered 295 pairs of 22 watt, 4 ft. high-output LED tubes, a pair for each fixture, with each pair to run on a single external driver. As I mentioned earlier, in their past life, each fixture held four T-12s and required 180 watts of power to operate. But, in my pre-order mockup, I demonstrated that a pair of these new LED tubes actually produced more footcandles of light on each desktop than four of the old clunkers.
These particular LED tubes are not powered to the end-pins; they’re powered directly to the tube. Although they come with dead-pins so they can be mounted in the old slots, they also come with easy-zip mounting clips so they can be installed symmetrically within the fixture between the slots - which the client preferred.
The simple savings is easy to calculate. At only 44 watts/fixture, we reduced consumption by 136 watts/fixture. With 295 fixtures, that’s a reduction of 40,120 watts! Even though they only operate 3754 hours/year, that’s an annual savings of over 150,610 kWh. At just over 11 cents/kWh, we saved them a whopping $16,869 a year in potential electricity bills.
But what really sold the client was the 2-year payback on their initial investment for an American-made product with a 10 year warranty.
Believe it or not, there are still millions of T12 tubes still being used in American buildings. Eventually the storage rooms and supply houses will run out of stock and the building owners will have to make a change. With such a large watt-reduction delta, even with the short run times and low utility rates I described here, relamping with LEDs makes good financial sense. For those in the Northeast corridor or out on the West Coast where utility rates are much higher, it’s a downright no-brainer for the client - and a nice moneymaker for the sales consultant who shows them the numbers.
I’m interested in similar stories and experiences.
Dallas Jones is President of Green Training USA.
